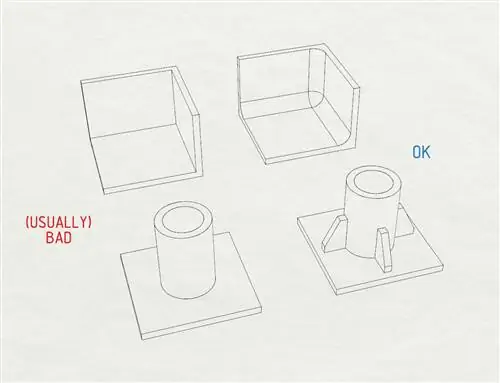
Достижения в области недорогой 3D-печати и обработки на станках с ЧПУ позволили растущему числу любителей проектировать и производить сложные детали, не выходя из дома. Но самой технологии не всегда достаточно: функциональные прототипы, изготовленные из PLA или изготовленные из HDPE, часто оказываются на удивление малой жесткостью и прочностью.
Интуитивной реакцией на эту проблему является равномерное увеличение размера или объема производимых компонентов, часто за счет времени печати, стоимости материалов или общей полезности и эстетики готовой детали. Когда такие компромиссы совершенно неприемлемы, некоторые домашние мастера вместо этого пытаются изготовить детали из более дорогих или сложных материалов, таких как алюминий или PEEK.
Как бывает, в большинстве случаев подобных разочарований можно полностью избежать. Производственная промышленность, всегда одержимая экономией времени и денег, разработала немало простых приемов, которые позволяют им легко приручать даже самые привередливые материалы и получать именно те результаты, которые они хотят. Чтобы во всем этом разобраться, давайте прогуляемся по некоторым из самых основных концепций проектирования и посмотрим, как они воплощаются в удивительно простые, но эффективные советы по проектированию деталей.
Удивительный мир изгибов
Технологические материалы, используемые в повседневной жизни, выходят из строя множеством способов, в зависимости от того, раздавливают ли их, разрывают на части, разрезают или подвергают каким-либо другим злоупотреблениям. Тем не менее, в мелкосерийном механическом прототипировании есть одна характеристика, которая почти всегда важнее остальных: способность деталей выдерживать изгиб.
Чтобы понять, почему детали ломаются при изгибе, давайте рассмотрим очень простой, но распространенный сценарий - прямоугольная балка, закрепленная на одном конце и подвергающаяся изгибающей силе (F) на другом:
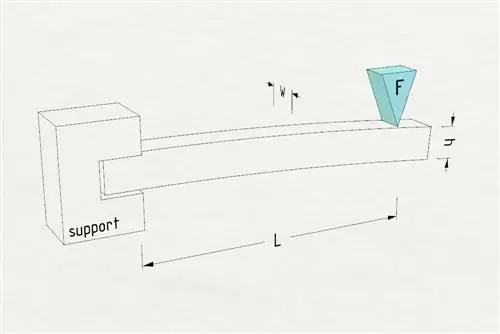
Изгиб консольной балки
Здравый смысл подсказывает, что сила, приложенная к лучу, будет оттягивать атомы вблизи верхней поверхности друг от друга и сжимать атомы на другой стороне. По мере увеличения нагрузки стресс, которому подвергаются эти молекулы, будет увеличиваться – до момента, когда он преодолеет электромагнитные силы, которые скрепляют все это вместе. Этот порог критического напряжения имеет тенденцию быть постоянным для конкретного типа материала, но в зависимости от того, сколько молекул в нем и какую форму они имеют, нагрузка, необходимая для достижения этой точки, будет разной.
Итак, как это происходит на практике? Начнем с того, что мы знаем, что внешние поверхности балки подвергаются наибольшему уровню растяжения и сжатия, и именно здесь напряжение будет наиболее выраженным. Немного упрощая, между этими областями существует линейный переход, образующий свободную от напряжений нейтральную ось, проходящую через центр поперечного сечения:
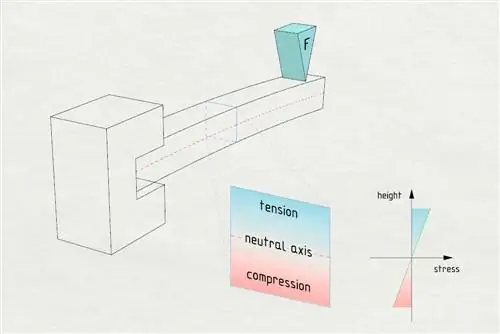
Распределение изгибающих напряжений, глядя на поперечное сечение прямоугольной балки.
Глядя на двухмерное поперечное сечение, нейтральная ось всегда перпендикулярна направлению приложенной силы. Для прямоугольников и других симметричных форм он пересекает середину балки; для других геометрий он проходит через центр тяжести площади, то есть геометрический «центр масс». Это местоположение может быть автоматически определено любой компетентной программой САПР; символьные формулы и калькуляторы для обычных сечений также легко найти в Интернете.
Существование области низких напряжений в центре балки интересно само по себе: возможно, оттуда можно намеренно удалить часть материала и использовать его для армирования внешних поверхностей с высокими напряжениями, чтобы в итоге мы получили более жесткую деталь, не увеличивая ее вес? Идея не такая уж безумная, как может показаться – именно так работают двутавровые балки:
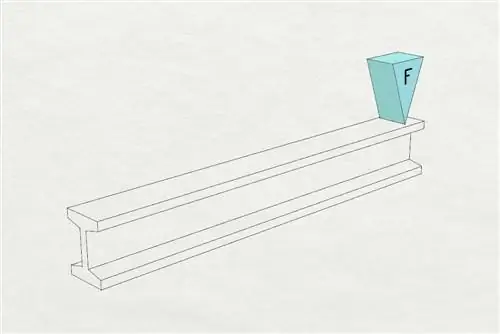
В строительстве двутавровые балки значительно превосходят прямоугольные балки, изготовленные из того же количества стали. С другой стороны, они более уязвимы к скручиванию, короблению и сдвигу, особенно если центральная часть слишком тонкая.
Но не будем забегать вперед. Когда дело доходит до распределения напряжений, следует иметь в виду еще одну вещь: пока их поперечное сечение постоянно, балки эффективно работают как простые рычаги, изгибающий момент которых пропорционален приложенной нагрузке и эффективному расстоянию. Таким образом, общее напряжение, испытываемое внутри консольной балки, также варьируется по ее деловой длине, начиная с нуля и линейно увеличиваясь до достижения точки крепления:
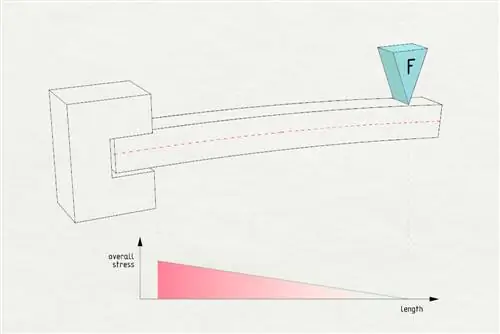
Распределение изгибающих напряжений по длине консольной балки.
Когда мы объединим два наблюдения, которые мы сделали до сих пор, мы можем сделать вывод, что наибольшее напряжение будет сосредоточено в очень специфическом месте нашей балки: на самой внешней поверхности рядом с местом крепления балки к другой конструкции.. Учитывая все это, попробуем разобраться, при каких условиях это напряжение выходит за пределы того, с чем может справиться материал.
Расчет напряжения изгиба
Основная экспериментальная формула для расчета максимального напряжения (σmax), присутствующая в нашей установке, выглядит следующим образом:
σmax=FLcx/ Ix
Давайте попробуем разобраться в этом: похоже, что напряжение на поверхности рядом с точкой крепления линейно пропорционально приложенной силе (F), умноженной на эффективную длину балки (L). Кроме того, оно пропорционально расстоянию между крайними точками поперечного сечения и нейтральной осью детали (cx), которое в прямоугольных балках равно h / 2. Все это должно быть достаточно ясно.
Что более загадочно, напряжение также обратно пропорционально величине, называемой моментом инерции площади (Ix), которая количественно определяет распределение материала относительно нейтральной оси балки. – эффективно описывающее, со сколькими молекулами придется бороться приложенной силе и насколько сильно они будут разорваны. Вывод формулы для этого параметра требует решения интеграла, но приложения САПР часто автоматизируют процесс поиска конкретных значений для спроектированных вами фигур; в противном случае онлайн-калькуляторы предлагают значения для стандартной геометрии балки для тех, кто в пути.
В любом случае формула для расчета момента инерции прямоугольной балки заданной высоты (h) и ширины (w) хорошо известна:
Ix=wh³ / 12
Если объединить все уравнения вместе, мы получим следующее уравнение для максимального напряжения в консольной прямоугольной балке:
σmax=6FL / (wh²)
На практике поставщики обычных материалов обычно проводят стандартизированные испытания на изгиб для расчета σmaxдля своей продукции; это значение затем указывается как прочность на изгиб в технических характеристиках. Поскольку мы обычно знаем значение σmax, давайте вместо этого решим уравнение для F; это даст нам максимальную силу, при которой ожидается выход компонента из строя, что кажется довольно полезной вещью. Общая формула:.
Fbreak=σmaxIx/ (Lcх)
Если подставить уравнения для Ixи cx в прямоугольные балки, мы получим такой вид:
Fbreak=⅙wh²σmax / L
Давайте попробуем это на практике: допустим, у вас есть кусок акрила шириной 1 см, толщиной 3 мм и длиной 10 см. Быстрый поиск показывает, что прочность акрила на изгиб составляет около 110 МПа (это 110 000 000 Н/м² или 110 Н/мм²). Итак, давайте посчитаем:
Fbreak=⅙10 мм(3 мм)²110 Н/мм² / 100 мм=16,5 Н ≈ 1,68 кгс
Похоже, что консольная нагрузка, приложенная к концу этой детали, не должна превышать примерно 1,6 кгс – и это без всякого запаса прочности. Если бы вы использовали полистирол (прочность на изгиб 40 МПа), то даже 0,6 кгс были бы серьезной проблемой. Ну и дела, кто бы мог подумать?
Оптимальная геометрия несущих деталей
Конечно, решать такие уравнения для каждого функционального компонента вашего проекта - это излишне; к тому же не все в жизни похоже на бревно, даже если очень сильно щуриться. Тем не менее, обсуждавшаяся до сих пор теория выделяет несколько удивительно универсальных стратегий проектирования, которые напрямую преобразуются в прочные и долговечные детали практически любой формы.
Как так? Что ж, давайте возьмем другой простой пример и предположим, что вы устраняете неполадки в механическом соединении, в котором используется пластиковый стержень толщиной около 1 мм и шириной 5 мм. Стержень продолжает ломаться при нагрузках, приложенных по оси X; Поразмыслив над проблемой, вы решаете увеличить ее несущую способность - бросок кубика - в три раза.
Как лучше всего достичь этой цели? Что ж, беглый взгляд на формулу для Fbreak в прямоугольных балках показывает, что существует линейная зависимость между шириной (w) и результирующим пределом нагрузки, поэтому очевидным выбором было бы утроить это значение. размер балки от 5 до 15 мм. С другой стороны, стержень теперь станет довольно громоздким; его вес и количество материала, необходимого для его изготовления, также увеличатся на 200%.
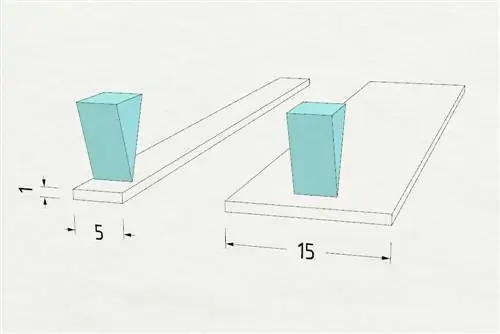
Утроение несущей способности балки, простой способ.
Конечно, мы можем добиться большего. Вышеупомянутая формула также говорит нам, что предельная нагрузка увеличивается пропорционально квадрату толщины детали (h). Другими словами, вам нужно высоту умножить всего на √3 ≈ 1,73 мм, чтобы получить трехкратное увеличение грузоподъемности. Такое изменение требует всего на 73 % больше материала и сохраняет деталь близкой к исходной форме:
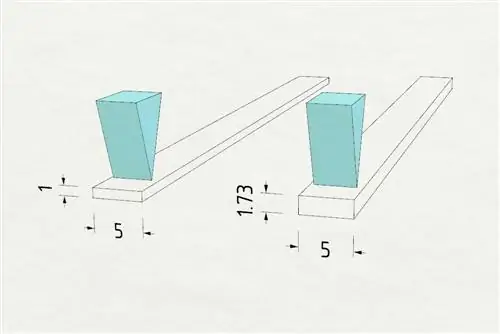
Лучший подход к проблеме: увеличение толщины детали.
На самом деле, даже этот подход довольно консервативен: если нет причин сохранять исходную ширину балки, мы могли бы сделать поперечное сечение квадратным, эффективно уравнивая его характеристики изгиба как по X, так и по Y. Если это так, то поперечное сечение может составлять всего 2,47 мм в ширину и 2,47 мм в высоту. Для этого решения требуется всего на 22% больше материала, чем для исходной балки 5 x 1 мм, но оно может выдержать нагрузку в три раза больше.
Но подождите, это еще не все: из-за того, что мы знаем о распределении изгибающих напряжений внутри поперечного сечения балки, у нас есть общее подозрение, что мы могли бы избавиться от части материала вблизи центра. формы без существенного ущерба для ее общих свойств при изгибе. Итак, давайте попробуем построить двутавровую балку, чтобы увидеть, каков будет практический эффект.
Чтобы понять, что произойдет, мы уже не можем смотреть на формулу для балок прямоугольного сечения; вместо этого нам придется вернуться к общей формуле для Fbreak:
Fbreak=σmaxIx/ (Lcх)
Поскольку двутавры симметричны, нейтральная ось всегда находится посередине, и, следовательно, cx=h/2. Единственное важное неизвестное - это Ix: символическую формулу для момента инерции площади можно легко найти в Интернете, но для этой конкретной формы луча она довольно беспорядочна; по этой причине лучше всего использовать программу САПР или онлайн-калькулятор, чтобы экспериментально выяснить, как изменяется значение Ixпри удалении секции посередине, а затем поэкспериментировать с тем, насколько сильно нужно ли нам добавить внешние фланцы, чтобы вернуться к желаемому значению Fbreak
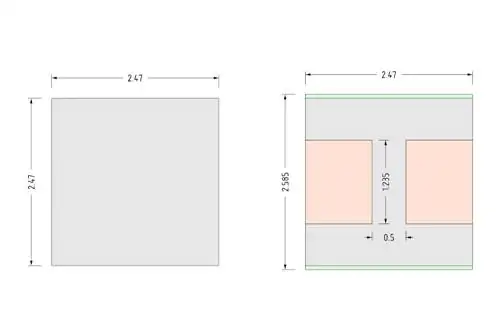
Построение двутавровой балки, соответствующей нашему предыдущему лучшему результату. Материал удаляется в красных областях, а затем выдавливаются зеленые секции до тех пор, пока расчетная максимальная нагрузка не будет соответствовать исходной форме.
В примере, показанном выше, нам пришлось добавить лишь незначительное количество материала на внешних поверхностях, чтобы компенсировать огромный подрез посередине. Фактически, в результате этого процесса была получена балка, которая имеет в три раза большую грузоподъемность, чем исходный стержень размером 5 x 1 мм, который пытаются заменить, но при этом использует на 20% меньше материала. Классно, да?
На практике двутавровые балки не являются обычным явлением в небольших масштабах, во многом потому, что их интеграция в геометрию детали усложнила бы большинство процессов производства скоб (скажем, литье под давлением или штамповку металла). Но если приглядеться, то можно заметить, что их близкие родственники - Т-образные балки и U-образные швеллеры - повсеместно встречаются в промышленном дизайне:
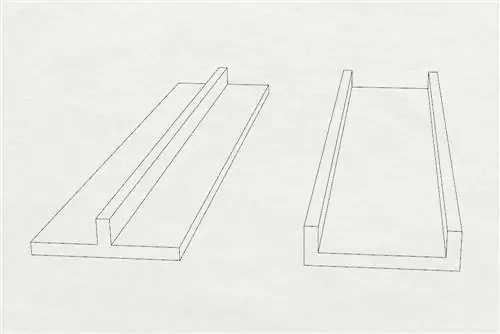
Распространенные способы армирования тонкостенных деталей. Профиль канала (справа) тоже можно закруглить.
Такие особенности обычно интегрированы в конструкцию самой детали: внутренние ребра, искусно изогнутые поверхности, крышки с фланцами, ободки и многие другие элементы современной индустриальной эстетики созданы не только для внешнего вида. Без них наши мобильные телефоны, корзины для хранения вещей и пластиковые стаканчики развалились бы сразу.
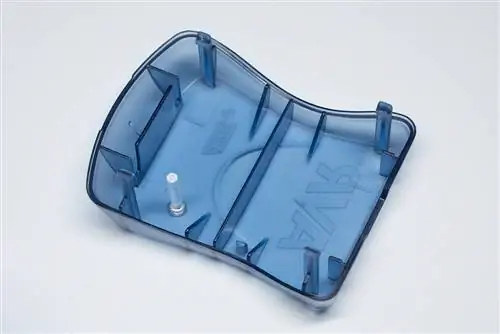
Широкое использование ребер жесткости и стенок продуманной формы в литом корпусе толщиной с бумагу для AVR ISP mkII, популярного программатора для микроконтроллеров ATmega.
Настройтесь на следующую неделю, чтобы увидеть вторую часть «Прототипы, которые живут долго». Во второй части мы поговорим о способах прогнозирования и контроля жесткости и ударопрочности распространенных материалов, используемых в 3D-печати и работе на станках с ЧПУ.